Investigadores de la Universidad de Rice han desarrollado un proceso energéticamente eficiente para convertir residuos plásticos en nanotubos de carbono y nanomateriales híbridos.
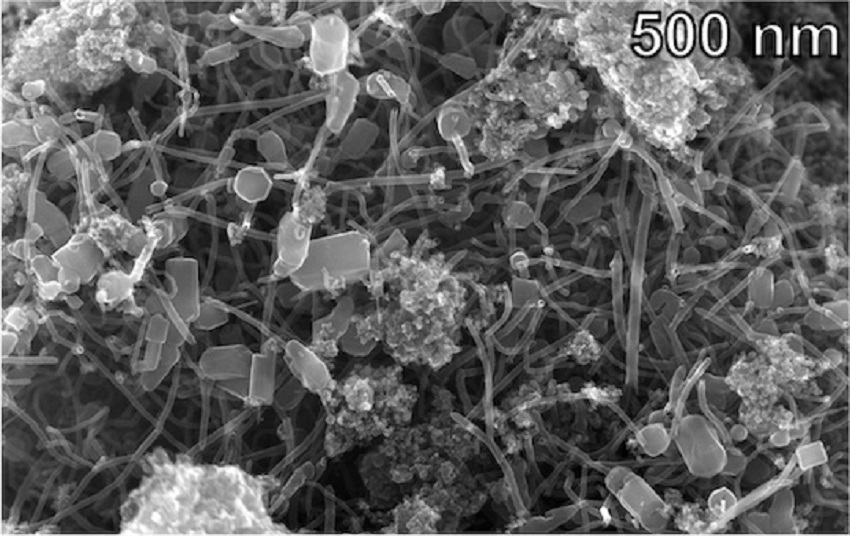
La cantidad de residuos plásticos producidos en el mundo se ha duplicado en las dos últimas décadas -y se prevé que la producción de plástico se triplique para 2050-, y la mayor parte acaba en vertederos, incinerada o mal gestionada de algún otro modo, según la Organización para la Cooperación y el Desarrollo Económicos (OCDE). Según algunas estimaciones, solo se recicla el 5%.
«Los residuos plásticos rara vez se reciclan porque cuesta mucho dinero lavarlos, clasificarlos y fundirlos para convertirlos en un material utilizable en una fábrica», explica Kevin Wyss, estudiante de posgrado de la Universidad de Rice, en Texas (EE.UU.) y autor principal de un estudio publicado en Advanced Materials que describe cómo él y sus colegas utilizaron su técnica de calentamiento flash Joule para convertir el plástico en valiosos nanotubos de carbono y nanomateriales híbridos.
«Pudimos fabricar un nanomaterial híbrido de carbono que superaba tanto al grafeno como a los nanotubos de carbono disponibles en el mercado», explica Wyss.
El grafeno, los nanotubos de carbono y otros nanomateriales basados en el carbono suelen ser fuertes y resistentes químicamente, tienen baja densidad y mucha superficie, y poseen conductividad y capacidad de absorción electromagnética de banda ancha. Esto los hace útiles en diversas aplicaciones industriales, médicas y electrónicas, como materiales compuestos, revestimientos, sensores y almacenamiento electroquímico de energía, entre otras.
«Lo realmente interesante de nuestros resultados esta vez es que hemos podido fabricar nanotubos de carbono con trozos de grafeno en los extremos», explica Wyss. Estos nanomateriales «normalmente son muy difíciles de fabricar, y el hecho de que hayamos podido hacerlo a partir de residuos plásticos es realmente especial».
La estructura del nuevo nanomaterial híbrido de carbono es responsable de su mayor rendimiento.
«Digamos que estoy intentando sacar un hilo de un jersey», explica Wyss. «Si el hilo es recto y liso, a veces puede salirse con bastante facilidad y estropear el tejido. Lo mismo ocurre con los nanotubos de carbono: tener estas masas de grafeno unidas en los extremos hace que sea mucho más difícil arrancarlas, lo que refuerza el compuesto».
«También se puede pensar de esta manera: Si te clavas una astilla, es fácil sacarla. Pero si te pinchas con algo que tiene una curva en el extremo, como un anzuelo de pesca, es mucho más difícil de sacar», añadió.
El plástico, que no necesita ser clasificado ni lavado como en el reciclaje tradicional, se «flashea» a temperaturas superiores a 3.100 grados Kelvin (unos 5.120 grados Fahrenheit). «Todo lo que hacemos es moler el material en trozos pequeños, del tamaño de un confeti, añadir un poco de hierro y mezclar una pequeña cantidad de otro carbono, por ejemplo carbón, para aumentar la conductividad», explica Wyss.
«Reciclar plástico cuesta más que producir plástico nuevo», añadie el investigador. «Hay muy pocos incentivos económicos para reciclar plástico. Por eso hemos optado por el upcycling, es decir, convertir materiales de desecho de poco valor en algo con un valor monetario o de uso más elevado. Si podemos convertir los residuos plásticos en algo más valioso, se puede ganar dinero siendo responsable en el tratamiento de los plásticos desechados».
Un análisis del ciclo de vida del proceso de producción reveló que el calentamiento flash Joule era considerablemente más eficiente desde el punto de vista energético y más respetuoso con el medio ambiente que los procesos de producción de nanotubos existentes.
«Comparado con los métodos comerciales de producción de nanotubos de carbono que se utilizan actualmente, el nuestro utiliza un 90% menos de energía y genera entre un 90% y un 94% menos de dióxido de carbono», concluye Wyss.