Los expertos del Laboratorio de Berkeley han publicado un trabajo en el que exponen las ventajas de usar este nuevo material, denominado PDK, capaz de competir en el mercado con los plásticos obtenidos a partir de resinas vírgenes.
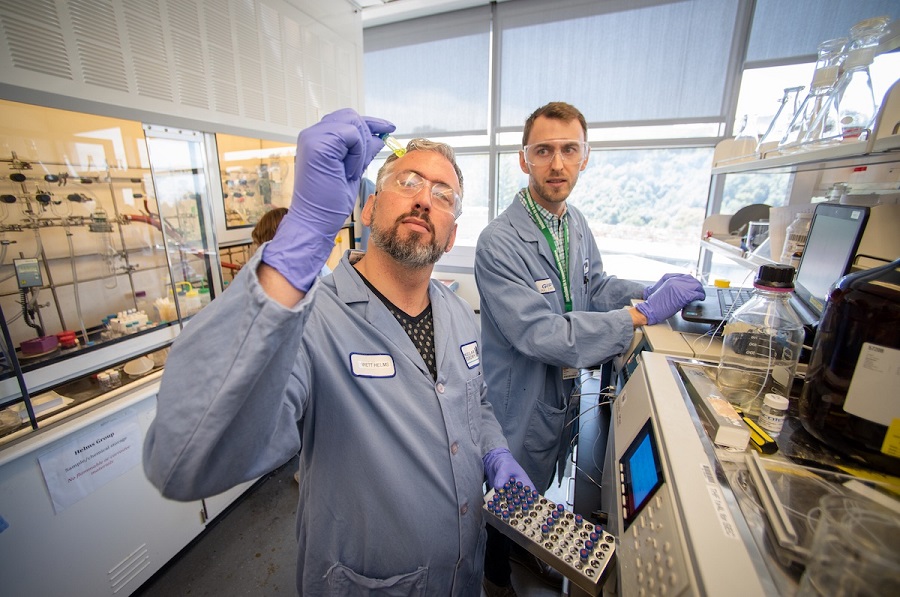
Hace menos de dos años, investigadores de Berkeley Lab (EE.UU.) anunciaron el desarrollo de un nuevo plástico que podría hacer frente a la crisis de los residuos. Denominado poli(diketoenamina), o PDK, este material tiene todas las propiedades convenientes de los plásticos tradicionales, pero evita los escollos medioambientales, porque a diferencia de los plásticos tradicionales, los PDK pueden reciclarse indefinidamente sin pérdida de calidad.
Ahora, el equipo de investigación de este centro perteneciente al Departamento de Energía norteamericano, ha publicado un estudio que muestra lo que se puede conseguir si los fabricantes empiezan a utilizar los PDK a gran escala. Aseguran que el plástico a base de PDK podría llegar a ser rápidamente competitivo desde el punto de vista comercial con los plásticos convencionales, y los productos serían menos costosos y más sostenibles con el paso del tiempo.
«Los plásticos nunca se diseñaron para ser reciclados. La necesidad de hacerlo se reconoció mucho después», explica Nemi Vora, una de las autoras del informe. «Pero impulsar la sostenibilidad es el núcleo de este proyecto. Los PDK se diseñaron para ser reciclados desde el principio». El equipo ha trabajado para perfeccionar los procesos de producción y reciclaje de los PDK, «de modo que el material pudiera ser lo suficientemente barato y fácil de utilizar a escala comercial en cualquier cosa, desde los envases hasta los coches».
El estudio presenta una simulación de una instalación de 20.000 toneladas métricas al año que produce nuevos PDK y recibe residuos de PDK usados para su reciclaje. Los autores calcularon los insumos químicos y la tecnología necesaria, así como los costes y las emisiones de gases de efecto invernadero, y luego compararon sus resultados con las cifras equivalentes de la producción de plásticos convencionales.
«Hoy en día, hay un gran impulso para adoptar prácticas de economía circular en la industria. Todo el mundo intenta reciclar todo lo que saca al mercado», explica Vora. «Empezamos a hablar con la industria sobre el despliegue de plásticos 100% reciclados de forma infinita y hemos recibido mucho interés».
«Las preguntas son cuánto costará, cuál será el impacto en el uso de la energía y las emisiones, y cómo llegar allí desde donde estamos hoy», añade Brett Helms, científico del Laboratorio de Berkeley. «La siguiente fase de nuestra colaboración consiste en responder a estas preguntas».
Superar las limitaciones del reciclado mecánico
Hasta la fecha, se han producido más de 8.300 millones de toneladas métricas de material plástico, y la gran mayoría ha acabado en vertederos o plantas de incineración de residuos. Una pequeña proporción de plásticos se envía a reciclar mecánicamente, es decir, se funden y se vuelven a transformar en nuevos productos. Sin embargo, esta técnica tiene un efecto limitado.
La propia resina de plástico está formada por muchas moléculas idénticas (llamadas monómeros) unidas en largas cadenas (polímeros). Pero para dar al plástico sus múltiples texturas, colores y capacidades, se añaden a la resina aditivos como pigmentos, estabilizadores térmicos o retardantes de llama. Cuando se funden muchos plásticos juntos, los polímeros se mezclan con un montón de aditivos potencialmente incompatibles, lo que da como resultado un nuevo material con una calidad mucho menor que la resina virgen recién producida a partir de materias primas. Por ello, menos del 10% del plástico se recicla mecánicamente más de una vez, y el plástico reciclado suele contener también resina virgen para compensar la disminución de la calidad.
Los plásticos PDK evitarían por completo este problema: los polímeros de resina están diseñados para descomponerse fácilmente en monómeros individuales cuando se mezclan con un ácido. Los monómeros pueden separarse de los aditivos y volver a reunirse para fabricar nuevos plásticos sin pérdida de calidad. Las investigaciones anteriores del equipo demuestran que este proceso de reciclaje químico consume poca energía y emite poco dióxido de carbono, y puede repetirse indefinidamente, creando un ciclo de vida de los materiales completamente circular.
Competir con la resina virgen
Sin embargo, a pesar de estas propiedades, para superar a los plásticos convencionales en su propio terreno, los PDK también tienen que tener las propiedades adecuadas. Reciclar el plástico tradicional a base de petróleo puede ser difícil, pero fabricar un nuevo plástico es muy fácil.
«Estamos hablando de materiales que básicamente no se reciclan», dice Corinne Scown, autora principal del trabajo. «Así que, en términos de atractivo para los fabricantes, los PDK no compiten con el plástico reciclado, sino con la resina virgen. Y nos alegró mucho ver lo barato y eficiente que será reciclar el material».
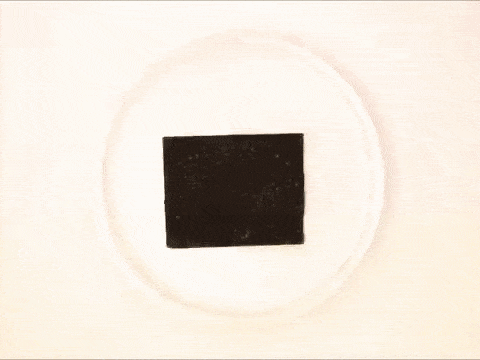
Scown, científica en las áreas de tecnologías energéticas y biociencias del Laboratorio de Berkeley, está especializada en la elaboración de modelos de las futuras repercusiones medioambientales y financieras de las tecnologías emergentes. Ella y su equipo han trabajado en el proyecto PDK desde el principio, ayudando al grupo de químicos y científicos de fabricación de Brett Helms a elegir las materias primas, los disolventes, el equipo y las técnicas que darán lugar al producto más asequible y ecológico.
El informe del equipo, publicado en Science Advances, modela un proceso de producción y reciclaje de PDK a escala comercial basado en el estado actual de desarrollo del plástico. «Las principales conclusiones son que, una vez que se ha producido el PDK inicialmente y se ha introducido en el sistema, el coste y las emisiones de gases de efecto invernadero asociadas a la continuación del reciclado para obtener monómeros y fabricar nuevos productos podrían ser inferiores, o al menos iguales, a los de muchos polímeros convencionales», afirma Scown.
Automoción y electrónica, los principales mercados
Gracias a la optimización del modelado del proceso, los PDK reciclados ya están despertando el interés de las empresas que necesitan abastecerse de plástico. Con la vista puesta en el futuro, Helms y sus colegas han realizado estudios de mercado y se han reunido con representantes de la industria desde los primeros días del proyecto. Su trabajo demuestra que la mejor aplicación inicial para los PDK son los mercados en los que el fabricante reciba su producto al final de su vida útil, como la industria del automóvil (a través de intercambios y devoluciones) y la electrónica de consumo (a través de programas de residuos electrónicos). Estas empresas podrán entonces aprovechar las ventajas de los PDK 100% reciclables en su producto: sostenibilidad y ahorro a largo plazo.
«Sabemos que hay interés a ese nivel. Algunos países tienen planes para cobrar fuertes tasas a los productos de plástico que dependen de material no reciclado. Ese cambio supondrá un fuerte incentivo financiero para dejar de utilizar resinas vírgenes y debería impulsar una gran demanda de plásticos reciclados, añade Scown».
Tras introducirse en el mercado de productos duraderos, como los coches y los aparatos electrónicos, el equipo espera ampliar los PDK a productos de menor duración y de un solo uso, como los envases.
Un futuro que cierra el círculo
Mientras hacen planes para un lanzamiento comercial, los investigadores de Berkeley Lab también continúan su colaboración en el proceso de producción del PDK. Aunque ya se prevé que el coste del PDK reciclado sea competitivamente bajo, los científicos están trabajando en mejoras adicionales para reducir el coste del PDK virgen, de modo que las empresas no se vean disuadidas por el precio de la inversión inicial.
Además, Scown y Helms están colaborando con Jay Keasling, destacado biólogo sintético del Laboratorio de Berkeley y de la UC Berkeley, para diseñar un proceso de producción de polímeros de PDK con ingredientes precursores obtenidos usando microbios.»
«En el futuro, vamos a incorporar ese componente biológico -continúa Helms-, lo que significa que podemos empezar a entender los impactos de la transición de las materias primas convencionales a materias primas de base biológica únicas y posiblemente ventajosas que podrían ser más sostenibles a largo plazo sobre la base de la intensidad en energía, carbono o agua de su producción y reciclaje».